
Radon Mitigation System Inspection Checklist
This guide for the House of Horrors® in Boulder, Colorado, is currently being produced for self-guided tours.
The guide is based on and refers to the most recent International Residential Code (IRC), which can be found online at https://codes.iccsafe.org/public/collections/I-Codes.
VISUAL INSPECTION
Radon Mitigation System Type
The inspector shall describe the radon mitigation system as one of the following types:
-
active sub-slab depressurization;
-
passive sub-slab depressurization;
-
sump (pit) depressurization;
-
drain-tile depressurization;
-
sub-membrane depressurization;
-
hollow-block wall depressurization;
-
crawlspace depressurization; or
-
heat-recovery ventilation.
OBSERVATION #1:
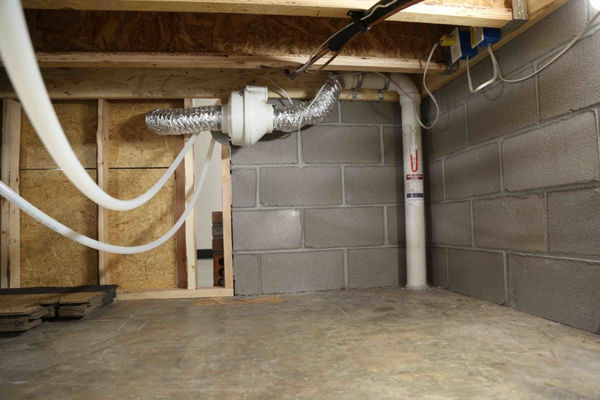
The radon system is an active sub-slab depressurization system.
Drain-Tile Depressurization Systems
The inspector should inspect drainpipes that extend to daylight for missing devices, such as one-way flow valves, or water traps that prevent outdoor air from entering the sub-slab area.
Sub-Membrane Depressurization Systems
The inspector should inspect the vapor retarder used for sub-membrane depressurization systems (passive or active) for seams that are lapped less than 12 inches, and edges that are not sealed to the walls, posts, or other penetrations.
Hollow-Block Wall Depressurization Systems
The inspector should inspect hollow-block walls for cracks, openings, and open top-courses.
Crawlspace Depressurization Systems
The inspector should inspect the crawlspace for the presence of asbestos-like material and combustible fuel-served appliances located within the crawlspace or in spaces adjacent to the crawlspace.
Heat-Recovery Ventilation (HRV) Systems
The inspector should inspect the area around the HRV system for the presence of asbestos-like material.
Piping and Fittings
The inspector should inspect for:
-
penetrations of pipes or ducts that penetrate a firewall or other fire resistance-rated wall or floor not protected in accordance with applicable building, mechanical, fire, or electrical codes;
-
submersible pumps not used in systems that use sump pits as the suction point for active soil depressurization if sump pumps are needed;
-
joints and connections that are not permanently sealed with adhesives;
-
joints and connections that are not airtight;
-
attic and external runs subject to sub-freezing that are not protected to prevent the risk of vent pipe freeze-up;
-
piping that is not PVC, ABS, or downspout (outside);
-
piping that is less than 4 inches in diameter;
-
piping subjected to weather or physical damage that is not Schedule 40;
-
pipe and fitting connections of different materials;
-
piping that isn’t solid and rigid;
-
reducers that are installed in the direction of air flow;
-
radon vent pipes blocking access to any areas requiring maintenance or inspection;
-
radon vent pipes not designed with removable or flexible couplings to facilitate removal of the sump pit cover for sump pump maintenance;
-
radon vent pipes not installed in a configuration that ensures that any rain water or condensation within the pipes drains downward into the ground beneath the slab or soil-gas retarder membrane; and
-
a missing one-way flow valve, water trap, or other control device installed in or on the discharge line to prevent outside air from entering the system while allowing water to flow out of the system when a radon mitigation system is designed to draw soil gas from a perimeter drain tile loop that discharges water through a drain line to daylight or to a soak-away.
OBSERVATION #2:

There are pipe connections that are not permanently sealed with adhesives.
OBSERVATION #3:

The external run is subject to sub-freezing and it is not protected to prevent the risk of vent pipe freeze-up. The piping is less than 4 inches in diameter.
OBSERVATION #4:
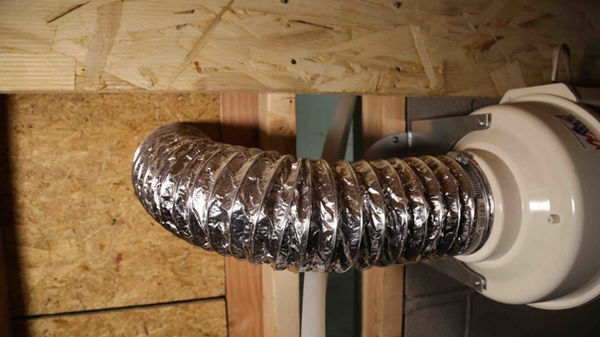
There is piping that is not PVC. It is not solid or rigid.
OBSERVATION #5:

There is a missing one-way flow valve, water trap, or other control device installed in or on the discharge line to prevent outside air from entering the system.
Piping Supports
The inspector shall inspect for:
-
hangers, strapping, or other supports that inadequately secure the vent material;
-
existing plumbing pipes, ducts, or mechanical equipment used to support or secure a radon vent pipe;
-
supports installed more than 6 feet apart on horizontal runs;
-
supports installed more than 8 feet apart on vertical runs; and
-
pipes not supported or not secured in a permanent manner so as to prevent their downward movement to the bottom of suction pits or sump pits, or into the soil beneath an aggregate layer under a slab to prevent blockage of air flow into the bottom of the radon vent pipes.
OBSERVATION #6:

There are hangers, strapping, or other supports that inadequately secure the vent material. A drywall screw is being used on the exterior clamp. The over-sized clamps in the crawlspace are not holding the pipe securely.
Materials
The inspector shall inspect for:
-
vent pipes not made of Schedule 20 PVC, ABS, or equivalent;
-
vent pipes used in garages and in other internal and external locations subject to weathering or physical damage not made of Schedule 40 piping or its equivalent;
-
vent pipe fittings in a mitigation system that are not of the same material as the vent pipes;
-
cleaning solvents and adhesives to join plastic pipes and fittings that are not recommended by the manufacturers of the pipe material;
-
improperly used caulks and sealants at any cracks in slabs or other openings around penetrations of the slab and foundation walls;
-
non-shrink mortar, grout, or expanding foam not being used when sealing holes for plumbing rough-in or other large openings in slabs and foundation walls that are below the ground surface;
-
sump pit covers not made of durable plastic;
-
sump pit covers not providing an airtight seal;
-
penetrations of sump covers that are not airtight;
-
plastic sheeting installed in crawlspaces as soil-gas retarders that are not a minimum of 6-mil polyethylene or equivalent material; and
-
any wood used in attaching soil-gas retarder membranes to walls or piers not pressure-treated or naturally resistant to decay and termites.
Point of Discharge for Fan-Powered Soil Depressurization and Block-Wall Depressurization Systems
The inspector should inspect for:
-
the point of discharge being below the eaves of the roof;
-
the point of discharge being less than 10 feet above ground level;
-
the point of discharge being less than 10 feet away from any window, door, or other opening into conditioned spaces of the structure that is less than 2 feet below the exhaust point; and
-
the point of discharge being less than 10 feet away from any opening into an adjacent building.
OBSERVATION #7:

The point of discharge is below the eaves of the roof. The point of discharge is less than 10 feet above ground level.
Radon Fan
The inspector should inspect for:
-
radon fans not designed or not sealed to reduce the potential for leakage of soil gas from the fan housing;
-
radon fans not sized to provide the pressure difference and air flow characteristics necessary to achieve the radon reduction goals established;
-
radon fans installed in the conditioned space of a building, in any basement, crawlspace, or other interior location directly beneath the conditioned spaces of a building;
-
radon fans installed in attics that are suitable for occupancy;
-
radon fans installed in attached garages beneath conditioned spaces;
-
radon fans installed underground;
-
radon fans installed in a configuration that allows condensation to build up in the fan housing;
-
radon fans that are not mounted vertically;
-
radon fans mounted on the exterior of buildings that are not rated for outdoor use or not installed in a watertight protective housing;
-
radon fans that are not mounted and secured in a manner that minimizes transfer of vibration to the structural framing of the building;
-
radon fans that are not installed using removable couplings or flexible connections to facilitate maintenance and future replacement; and
-
radon fans used in crawlspace pressurization or building pressurization that do not have removable screens or filters on the fan intakes to prevent ingestion of debris or personal injury.
OBSERVATION #8:

The radon fan is installed in the crawlspace, directly beneath the conditioned spaces of a building.
OBSERVATION #9:

The radon fan is not mounted vertically. The radon fan is installed in the wrong direction. The fan is not labeled as a fan manufactured for a radon system. The fan is used as a bathroom exhaust fan.
Suction Pit for Sub-Slab Depressurization Systems
The inspector should inspect for:
-
an inadequate amount of excavated material from the area immediately below the slab penetration point of the system’s vent pipes.
Sealing
The inspector should inspect for:
-
uncovered or unsealed sump pits that permit entry of soil gas or that would allow conditioned air to be drawn into a sub-slab depressurization system;
-
openings around radon vent pipe penetrations of the slab, foundation wall, or crawlspace soil-gas retarder membrane that are not cleaned, prepared and sealed in a permanent, airtight manner;
-
open or unsealed openings in the tops of walls and all accessible openings or cracks in the interior surfaces of the walls, where a block-wall depressurization system is used to mitigate radon;
-
openings, perimeter channel drains, or cracks where the slab meets the foundation wall that are not sealed;
-
seams and joints in the baseboard of baseboard-type suction systems that are not joined and not sealed;
-
seams in soil-gas retarder membranes used in sub-membrane depressurization system that are not overlapped at least 12 inches and not sealed;
-
open and unsealed access doors and other openings between the basement and the adjacent crawlspace where the crawlspace has been confirmed as a source of radon entry; and
-
open and unsealed openings and cracks in floors above the crawlspace that would permit conditioned air to pass out of the living spaces when crawlspace depressurization is used.
OBSERVATION #10:
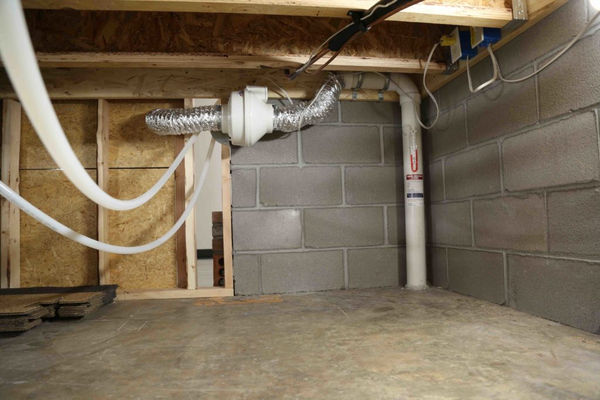
There are openings around radon vent pipe penetration of the slab that are not cleaned, prepared and sealed in a permanent, airtight manner. There are cracks where the slab meets the foundation wall that are not sealed.
OBSERVATION #11:
There are open and unsealed access doors and other openings between the house and the adjacent crawlspace where the crawlspace has been confirmed as a source of radon entry.
Electrical
The inspector should inspect for:
-
wiring that does not conform to provisions of the National Electrical Code (NEC) and local building codes;
-
wiring located in or chased through ducting;
-
cord and plug assemblies supplying power to radon fans that are more than 6 feet in length;
-
cord and plug assemblies supplying power to radon fans that pass through walls, floors or ceilings, or that are concealed within building components;
-
radon fans installed on the exterior of the building that are not hard-wired into an electrical circuit;
-
radon fans used outdoors that are plugged;
-
a missing electrical disconnect switch or a missing circuit breaker for radon mitigation system fan circuits;
-
a means of disconnect not in sight of its radon fan;
-
missing grounded receptacles (required within 6 feet of radon fans installed under roofs);
-
missing GFCI receptacles (required within 6 feet of radon fans installed above roofs); and
-
missing electrical junction boxes (required within 6 feet of radon fan locations of both active and passive systems).
OBSERVATION #12:
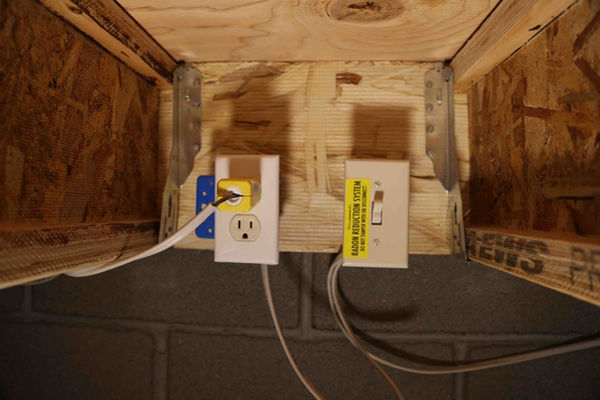
There is wiring that does not conform to provisions of the National Electrical Code (NEC) and local building codes. The system is connected to a wall switch in the garage located near the crawlspace access doorway.
OBSERVATION #13:

The radon fan should be installed on the exterior of the building, and it should be hard-wired into an electrical circuit. There are hazards conditions at the electrical switch and plug. Missing GFCI-protection at the receptacle. There is loose wiring hanging and wrapped around the piping.
Drain
The inspector should inspect for:
-
condensate drainpipes that are not directed into condensate pumps, not directed into trapped floor drains, or do not have 6-inch or greater standing water-trap seals;
-
unsealed perimeter (channel or French) drains; and
-
a sump pit (used for protection or relief from excess surface water) that has a cover not recessed and not fitted with a trapped drain.
HVAC
The inspector should inspect for:
-
modifications to an existing HVAC system proposed to mitigate elevated levels of radon that are reviewed and approved by a qualified contractor;
-
foundation vents (used to reduce indoor radon levels by increasing natural ventilation) that are closable;
-
heat-recovery ventilation (HRV) systems that are installed in rooms that contain friable asbestos;
-
supply and exhaust ports of heat-recovery ventilation systems installed less than 12 feet apart; and
-
confirmation by the contractor that the incoming and outgoing flow from heat-recovery ventilation systems are balanced.
Monitoring and Labeling
The inspector should inspect for:
-
a missing mechanism to monitor performance of an active soil depressurization system and block-wall depressurization system and to warn of system failure;
-
electrical radon mitigation system monitors installed on switched circuits;
-
electrical radon mitigation system monitors not designed to re-set automatically when power is restored after failure;
-
manometer-type pressure gauges not clearly marked to indicate the range of pressure readings that existed when the system was initially activated;
-
a missing system description label placed on the mitigation system;
-
a missing system description label placed on the electric service entrance panel;
-
a system description label that is not legible from at least 3 feet away;
-
a system description label that does not include all of the following information:
-
“Radon Reduction System”;
-
the installer’s name and contact information;
-
the date of the installation; and
-
an advisory that the building should be tested for radon at least every two years;
-
-
a missing system description label on each floor level of all exposed and visible interior radon mitigation system vent-pipe sections reading “Radon Reduction System”;
-
missing identification of the circuit breaker controlling the circuit on which the radon vent fan and system-failure warning devices operate; and
-
missing labels on the plastic vapor barrier (if installed).
OBSERVATION #14:

There is a missing electrical radon mitigation system monitor installed on the switched circuit. The manometer-type pressure gauge is not clearly marked to indicate the range of pressure readings that existed when the system was initially activated.
OBSERVATION #15:
There is a missing system description label that should be placed on the electric service entrance panel.
OBSERVATION #16:

The system description label does not include the installer’s name and contact information and the date of the installation.
RADON CHECKLIST AND ONLINE COURSE:
InterNACHI has a free, online Advanced Radon Measurement Service Provider Course, which includes a radon system inspection checklist.
InterNACHI-Certified Radon Tester
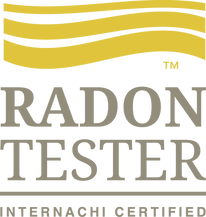